Top 10 Safety Practices For California Indoor Heat Compliance
Preventing heat illness and injury is critical for ensuring the safety and health of workers, particularly in high-risk environments like warehouses and distribution centers. As temperatures rise, the threat of heat-related incidents—such as heat exhaustion, heat stroke, and even fatalities—continues to grow. In response to these increasing risks, California recently updated its regulations to include a stricter indoor heat standard, mandating continuous monitoring of temperature, humidity, and the heat index. Compliance with these new standards is essential for protecting workers and preventing heat-related accidents, while also safeguarding companies from regulatory penalties. This guide outlines the top steps safety managers can take to meet these requirements and ensure both compliance and worker well-being.
Top 10 Things Safety Managers of California Warehouses Should Do to Ensure Worker Health, Safety, and Heat Standard Compliance:
1. Implement Heat Illness Prevention Programs
Follow California’s indoor heat standard by actively monitoring temperature, humidity, and heat index levels, especially for workers in confined or poorly ventilated spaces. Use of sensor based wearables can be extraordinarily advantageous for this application. Now sensors can move with the worker, rather than being stationary, ensuring accurate data for real-time heat tracking to preemptively prevent heat-related incidents.
2. Monitor Heat and Physical Strain in Real Time
Use sensor based wearable devices to continuously track not only heat conditions but also physical exertion. This helps ensure that workers aren’t overexerting themselves, especially during high-heat periods, reducing the risk of heat-related illness.
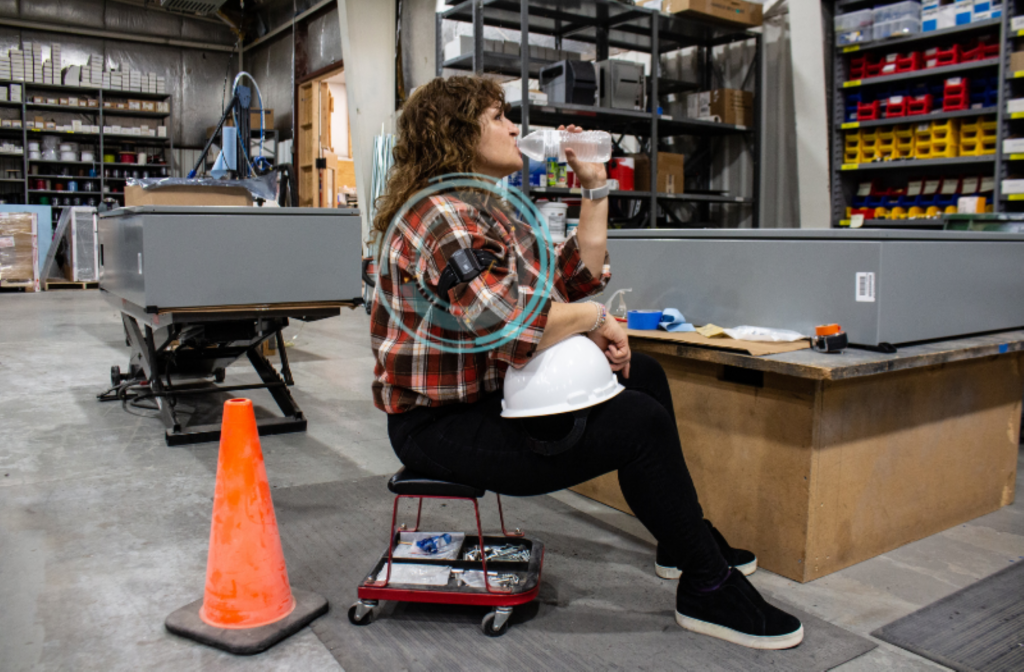
3. Ensure Adequate Hydration and Rest Breaks
Provide workers with easy access to water and encourage frequent hydration breaks. Schedule regular rest periods, particularly during high-heat times, and rotate workers to reduce exposure and physical strain.
4. Track Worker Acclimatization
Monitor new or returning workers for heat tolerance, as acclimatization is critical. Use real-time data to identify individuals at higher risk of heat stress and adjust work schedules or assignments as needed during the first few days of heat exposure.
5. Leverage Mobile Environmental Monitoring
Equip workers with wearable devices that act as mobile sensors, gathering environmental data from every part of the facility. This allows safety managers to identify hazardous zones and adjust work protocols accordingly.
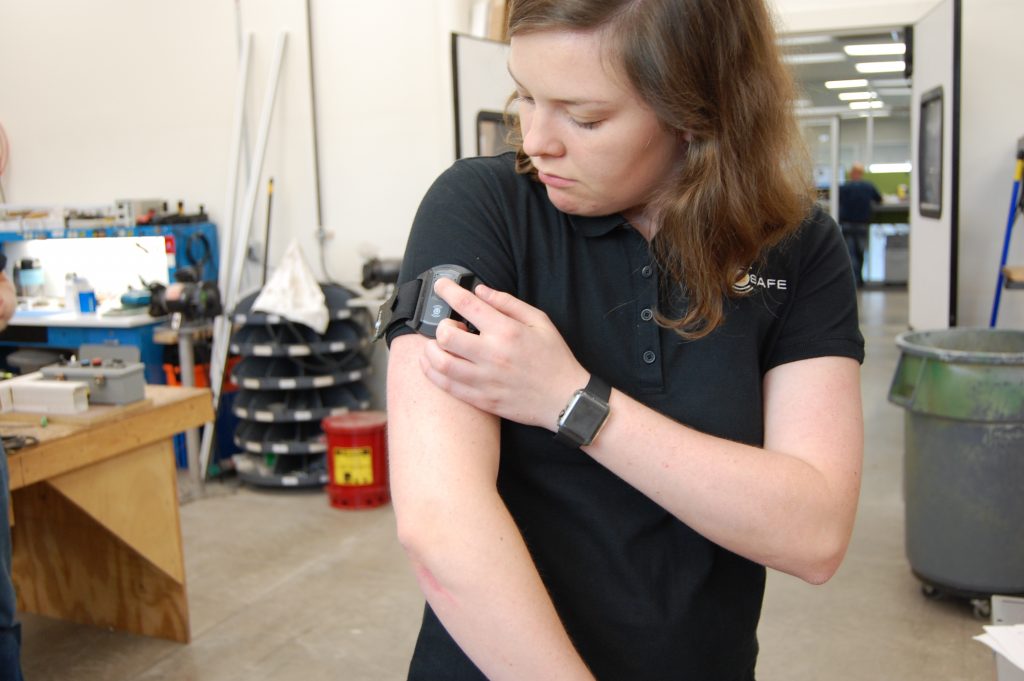
6. Use Push-to-Talk Communication
Ensure that workers can instantly report unsafe conditions, like equipment failures or high heat zones, using push-to-talk technology. Prompt communication enables faster responses to potential safety risks.
7. Document Compliance with Time-Stamped Data
Ensure compliance with OSHA and California regulations by documenting environmental conditions with time and location stamps. Gathering data about experiences and exposures, rather than the worker, enables evidence-based safety decisions and regulatory reporting.
8. Train Workers on Heat Illness Symptoms
Educate your team to recognize early signs of heat exhaustion or heat stroke, such as dizziness, confusion, and muscle cramps. Encourage immediate reporting of any symptoms, so proactive measures can be taken before conditions worsen.
9. Integrate Air Quality Monitoring
Use wearable technology to monitor not only heat but also air quality. Poor air quality can exacerbate heat stress, especially in workers using personal protective equipment (PPE). Sensors that move with the worker can monitor air quality in real-time where work is happening.
10. Ensure Privacy and Trust with Non-Invasive Monitoring
Foster trust among workers by using devices, which monitor environmental conditions rather than personal biometrics or continuously tracking the worker, ensuring privacy while providing essential safety data.
Learn More & Get Started!
If worker safety and management effectiveness are high priorities for you, let’s talk!
Download our flyer to learn more!
Additional Resources for Download
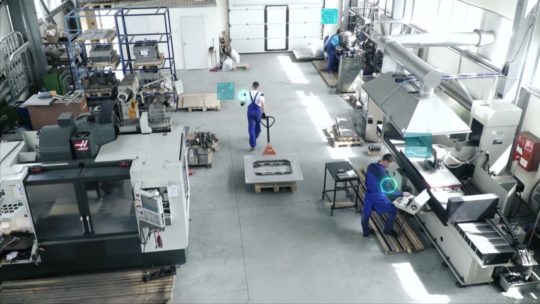
The MākuSafe® Model:
Leveraging predictive information and just-in-time solutions to keep workers safe
Learn more about how MākuSafe® is using workforce wearables to track, predict and prevent near-misses to keep workers safer.