MākuSafe Profiled in Des Moines Register
January 22, 2020
West Des Moines’ MakuSafe plans large 2020 expansion
Tyler Jett, Des Moines Register
Published 5:59 p.m. CT Jan. 21, 2020 | Updated 6:00 p.m. CT Jan. 21, 2020
Karen Yardley pulled up an app on her iPad every morning last summer, checking in on 18 workers at her company’s factory.
The app showed Yardley, a sanitation and safety manager at Crest Foods Co. Inc. in Ashton, Illinois, whether the workers could be in danger. Was the factory too hot? Too bright? Too loud?
For the most part, she said, everything looked fine on the app from MakuSafe, a West Des Moines startup. The company sells a wearable device, about the size of an iPod Classic or a beeper, that straps to workers’ biceps and tracks safety data.
MakuSafe, which ran a three-month pilot program last summer and plans a big rollout this year, uses a sensor inside the device to detect slips and trips. It also measures potentially dangerous motions like body twists. At Crest Foods, a dry-food packaging plant, Yardley said, the device registered repetitive motions that could cause long-term injuries.
MakuSafe also reports details like whether the space workers occupy is hot or humid and whether employees are falling in a particular spot.
Work inside the Crest Foods factory is physically taxing, Yardley said. Employees dump foods into vessels, package the product and stack crates.
“It put a spotlight on some things that we do, day in and day out, that we’ve just kind of grown accustomed to, and so have our employees,” Yardley said of MakuSafe’s app. “But while we were wearing the devices, it called it out: ‘Hey, this is a motion you should take a second look at. And if there’s a way you can engineer it out, take a look at it, get rid of it, you might want to.'”
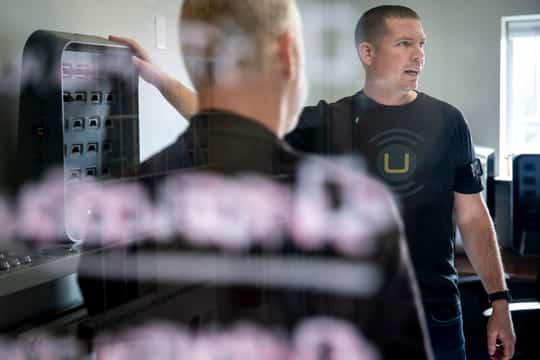
MakuSafe co-founder and CEO Gabe Gynn talks about a MakuSafe base station at the company’s offices in West Des Moines. (Photo: Brian Powers/The Register)
After going through the pilot last summer, MakuSafe CEO and co-founder Gabriel Glynn said he expects to receive the first shipments of the devices for a 2020 rollout in late January or early February. With $1.5 million in investor support this year,Glynn expects to sell 8,000 devices to 100 companies.
The startup is showing other signs of growth. Its operation has expanded from just one room the size of a foyer to a space with an office, a lab, a conference room and a loft for a software development team. It now has 12 employees, up from four a year ago — Glynn included.
The company’s model this year is to spread the devices, even in small numbers, to as many different businesses as possible. The hope is they will be impressed enough to buy more.
“In 2021, what does it look like if we can scale up within these companies?” Glynn said. “And that’s when we start to get really excited.”Get the Iowa Business Update newsletter in your inbox.
MakuSafe’s pilot program full of lessons
The son of a former machinist and safety manager,Glynn thought up MakuSafe while producing an advanced manufacturing podcast for the Iowa Association of Business and Industry. During a factory visit for one episode, he learned Occupational Safety and Health Administration inspectors were investigating a work site where an employee had recently lost hearing from machines that ran too loudly.
According to the Iowa Division of Labor, 42,500 workers suffered injuries on the job in 2018. Another 77 workers died. Glynn wanted to build a device that automatically detected hazards to protect employees — and save on workers’ compensation claims. After 3 1/2 years of development, he said MakuSafe picks up on a range of potential problems: ambient light level, temperature, humidity, noise, barometric pressure and air quality.
The ability to log workers’ slips and trips is particularly valuable. Safety managers miss important information because employees don’t always report their falls.
The data may help detect trends that prevent injuries or deaths. A safety manager using the program may notice workers slipping more on summer afternoons, when high humidity creates more condensation. Or a couple workers may slip in the same place on the same morning, an indicator that a particular corner of the factory is slippery from a spill.
While MakuSafe had tested the device in central Iowa factories, Glynn said last summer’s pilot was important for a couple of reasons. First, the company was using an initial shipment of the device from its overseas manufacturer. Co-founder and Chief Technology Officer Mark Frederick previously had fastened the devices together by hand in his basement. Glynn and Frederick wanted to know how the cheaper, mass-produced product held up on factory floors.
Second, MakuSafe had never operated so many devices at the same time. With 120 devices in the field last summer, a MakuSafe customer relations representative tracked workers at six different locations at once. When he got alerts on the company dashboard, he called the local safety managers to confirm they saw the problems on the ground. For the most part, the devices worked.
The pilot exposed some issues, though. Frederick said some data didn’t automatically transfer to MakuSafe’s cloud-based software. The devices also didn’t connect in their charging stations overnight because of a small design flaw. Frederick said the company fixed both problems.
In addition, MakuSafe’s hardware also didn’t detect air quality issues at a specific enough level for some locations. The device is supposed to tell how much carbon dioxide and total volatile organic compounds are in the air and inform companies’ safety managers whether the environment has become dangerous for workers.
At Crest Foods, Yardley said, MakuSafe devices alerted her that there may be a problem with the air quality. But the device didn’t explain what, specifically, was wrong.
Glynn said companies should use the sensor to track the air quality every day. If a reading changes dramatically, they should alert an inspector with a high-quality sensor to get more detailed information.
Overall, Yardley was pleased with the product. Workers didn’t complain that it was a burden to wear the device during their shifts. The devices withstood some tough environments like a boiler room and the wash bay.
One device stopped working after an employee accidentally brought it home and washed it with his clothes.
“But other than that,” Yardley said, “they held up well.”
Emerging technology in the ‘near miss’ industry
At its heart, MakuSafe’s value comes from its ability to identify what safety managers call “near misses,” said Bryon Snethen, the vice president of risk improvement at Des Moines-based EMC Insurance, an investor in the startup. A “near miss” is any time a worker almost gets hurt or almost causes damage to the work site.
These incidents are difficult to track. While some safety managers try to encourage workers to report as many problems as they can, it’s hard to know what doesn’t get reported. To make reporting easier, EMC created an app that allows workers to send messages about potential problems on their phones.
But even that process has problems, Snethen said. Most factories don’t let workers bring their phones onto the floor.
Snethen said MakuSafe can improve reporting in a couple of ways. The device’s motion sensor should automatically report all falls, as well as unusual movement. The device also has a microphone that allows workers to send 15-second audio messages to safety managers.
“I think it’s going to change the game,” Snethen said.